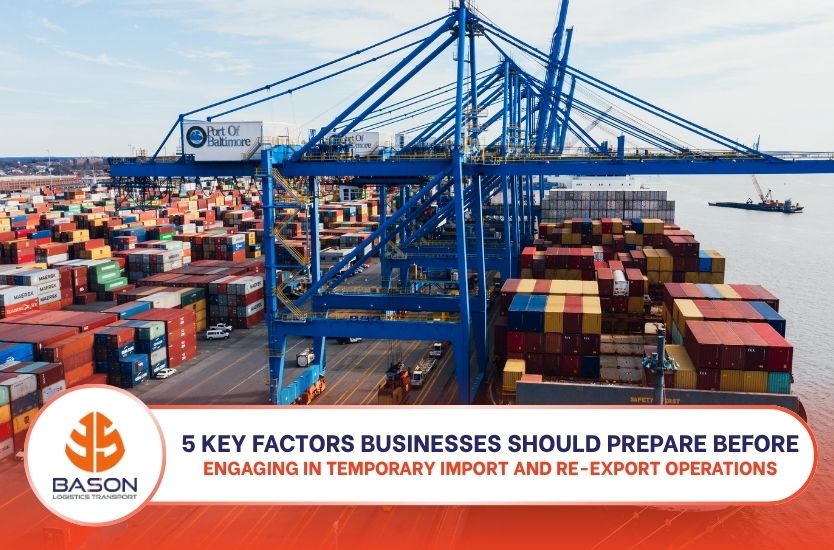
Temporary import and re-export is a complex business that demands meticulous preparation – from documentation to logistics and partner coordination. Below are the key elements every business must get right to ensure smooth and compliant operations.
Understand the legal regulations and eligible goods for temporary import and re-export
Types of goods eligible for temporary import and re-export
In temporary import and re-export operations, businesses must note that not every type of cargo qualifies for this scheme. Commonly approved categories include electronics, machinery, industrial components, consumer-grade raw materials, and selected garments.
For more sensitive or regulated goods—such as chemicals, pharmaceuticals, and medical equipment—enterprises are required to obtain specific sectoral permits or comply with dedicated regulations outlined in current circulars. Failing to meet these requirements may result in customs delays or legal risks, so careful review and preparation are essential before initiating any shipment.
Regulations on storage duration and inventory control
Goods brought in under temporary import arrangements may be stored in bonded warehouses for up to 12 months. Extensions are permitted when there is a valid reason, but these must follow the correct procedures and receive official approval from customs authorities.
Additionally, businesses are required to submit regular reports and maintain clear, well-organised records of their cargo flow to ensure transparency and compliance during inspections by relevant authorities.
2. Strict control over documentation and customs procedures.
All documentation must be complete, timely, and aligned with commercial logic.
Operating under a temporary import–re-export model requires a fully prepared set of customs documents, including the commercial contract, invoice, packing list, bill of lading (B/L), and any accompanying permits where applicable.
These documents must be consistent in terms of figures, product specifications, delivery terms, and re-export timelines. Even a minor discrepancy can result in delays for the entire shipment.
The importance of customs inspection and handling information discrepancies.
Customs inspection is a critical step, especially for high-risk goods or shipments with a history of non-compliance. If declared information does not match the actual cargo, the shipment may be held for verification, leading to additional costs such as container detention, warehousing fees, or even administrative penalties.
That’s why conducting an internal inspection before the official customs check is an essential part of any professional temporary import–re-export process.
3. Selecting the right bonded warehouse and transport route.
The warehouse should be located near the port and capable of handling technical goods.
Choosing a warehouse located near seaports or key trade hubs helps shorten delivery times and reduce transshipment costs. Beyond location, the facility must be equipped to handle technical goods—offering services such as sorting, counting, repacking, and batch-based storage. These capabilities are essential to ensure the cargo is ready for re-export without technical setbacks.
The transport route must be reliable and ensure compliance with re-export commitments.
In temporary import–re-export operations, the re-export timeline is often pre-defined in contracts or agreements with partners. This makes it critical to work with a transport provider that offers reliable schedules and can respond quickly to unexpected changes.
Delays beyond the permitted storage period may lead to administrative violations, unnecessary costs, or in severe cases, forced disposal of the goods if re-export cannot be completed on time.
4. Trade and logistics partners must demonstrate proven capabilities and hands-on experience
A logistics provider must have a strong understanding of customs procedures
A professional logistics partner must not only offer appropriate warehousing infrastructure, but also be capable of working directly with customs, shipping lines, and port authorities to expedite procedures. Practical experience in temporary import and re-export enables the provider to anticipate potential risks related to documentation, inspection, or transit — and proactively propose effective solutions
A trade partner must demonstrate legal transparency and provide clear, reliable payment terms
Businesses must also ensure that the re-export buyer holds proper legal status and can fulfill payment obligations on time. Contracts should clearly define delivery terms, quantity commitments, and timelines to prevent situations where goods are left in limbo due to buyer delays or withdrawal from the agreement.
5. Risk preparedness and contingency planning in place
Develop a response plan in case goods are rejected and cannot be re-exported
In certain cases where the buyer refuses to accept the goods as agreed, the business must be prepared with an early response plan. If permitted by law, the goods may be converted from temporary import for re-export to import for domestic sale. However, this requires a complex process and prior approval from customs authorities. Therefore, it is best to have contingency measures in place from the outset.
Closely monitor storage duration and all relevant permits
To avoid risks related to warehouse overstays, businesses should establish an internal alert system with task reminders and assign personnel to track each shipment in real time. This is an effective way to prevent missed deadlines, loss of re-export rights, or administrative penalties due to regulatory violations.
Bason – A logistics partner with deep expertise in temporary import and re-export operations
Proven Experience in documentation handling
With years of working alongside industrial and trading businesses, Bason Logistics has built solid, hands-on experience in handling temporary import and re-export (TNTX) documentation — from selecting the correct HS codes and coordinating customs inspections, to preparing complete document sets including CO, CQ, invoices, and packing lists.
Our in-depth understanding of customs procedures and trade logic allows us to work efficiently with the customs system, minimize common errors, and ensure goods are processed quickly and in full compliance.
Bonded Warehouse Near the Port
Bason’s bonded warehouse is strategically located in Thu Duc City, near Cat Lai Port, making it ideal for storage, consolidation, and re-export operations. The warehouse is clearly zoned for different functions, allowing for batch classification and repacking if needed — especially suitable for technical goods or items requiring special storage conditions.
Inventory is tracked by batch code with transparent updates, enabling tight control over stock flow throughout the entire storage period.
Proactive Transport and Full-Process Monitoring
Beyond warehousing, Bason offers synchronized inland trucking and container transport services integrated with TNTX operations. From the moment goods arrive at the port to the point of re-export, every step is tracked in real time via operational reports. This allows clients to monitor progress and coordinate shipments proactively — without leaving things to chance.
TNTX is more than just a logistics task — it’s a high-precision operation that demands close coordination across legal compliance, documentation, storage, customs inspection, and transport. To avoid unnecessary risks and costs, businesses need the right partner — one with both the system and the people to ensure a seamless process.
Contact:
- Address: M Floor, 104 Bat Nan Street, Binh Trung Ward, Ho Chi Minh City, Vietnam
- Email: sales@bason.vn
- Hotline: 0869 456 077